Fostering Grassroots Improvement: The Brighter Ideas Program
Spartronics Brooksville fosters internal, continuous improvement through their Brighter Ideas Program
Proactive organizations constantly search for ways to improve their processes, employee engagement, and productivity. However, strong organizations understand that by empowering their employees as professionals, engagement, productivity, and improved processes easily follow suit. At Spartronics, we aim to foster an environment of bottom-up improvement that encourages our employees to become leaders and thought starters daily. For that reason, Spartronics Brooksville relaunched the Brighter Ideas program.
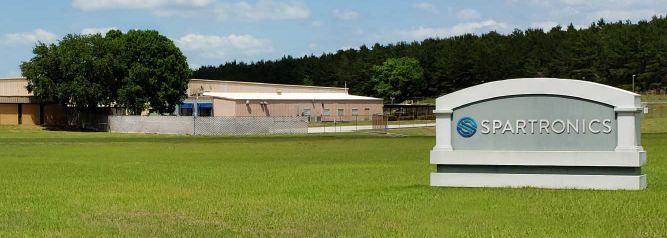
Setting the Foundation for Continued Improvement
The Spartronics Brooksville Brighter Ideas program was a reincarnation of a previous program the facility had implemented in 2013 but was not seeing much success. While the initial program encouraged employees to develop new ideas, it was more of a "suggestion box" submission with a months-long turnaround and committee review process. Due to this, employee engagement was meager, and interest in the program had wavered throughout the years.
Understanding something had to be done, Continuous Improvement Manager, Marc Macintosh, set out to revamp the program upon his arrival in 2019. He teamed with several of the site's functional managers and began researching where the program was lacking and how to improve it. Alongside his colleagues, Macintosh took this as an opportunity to foster a culture of continuous improvement amongst all the Brooksville employees while leveraging support from the Brooksville site leadership team. During his research, he performed countless employee focus groups and captured feedback to understand the current program. He then mapped a much more effective and quicker process for the program. After months of conducting these initiatives, the new Brighter Ideas program was launched in July 2019.
Fostering Improvement Through Brighter Ideas
Macintosh and his team wanted the Brighter Ideas program to be an employee-led initiative focused on implementing lean concepts like reducing waste and improving flow, focusing on problems within that functional area, and executing low-cost, "quick win" changes. They also wanted to empower employees to take ownership of their ideas to improve their job and to drive implementation as Idea Leads, which would, in turn, help improve the business. Since the relaunch, the program has reduced idea approval times from 30 days to only 24-48 hours while ensuring the idea complies with customer and regulatory requirements. This improved responsiveness reinforced leadership interest in all ideas to improve quality, increase on-time delivery, and reduce cost.
One example of an implemented idea came from a critical-skilled Quality Inspector who identified they were spending too much time walking to the scanner daily. The Quality Inspector, who became the Idea Lead, noted that they were traveling over 1 mile per day to scan quality documents required by the customer. The Idea Lead documented the problem they were trying to solve and who else was needed to help solve it. The Idea Lead was then coached throughout the entire process as they mapped the process and brainstormed solutions. Ultimately, they uncovered that the solution was to install a scanner in their work area while removing another unused printer to offset the cost. This simple example is just one that represents how Spartronics Brooksville managers and supervisors support Idea Leads and empower them to put their ideas into action.
The idea implementation process is about 60 days from beginning to end. There is a 30-day validation period following implementation to assess how the solution is going and ensure that it fits the functional area. During this period, the Idea Lead is provided feedback, and the cost savings are calculated. As feedback is one of the most valuable learning tools, the program ensures it is always delivered to help foster growth from Spartronics Brooksville employees.
To recognize their hard work, employees share their ideas and outcomes at the monthly Brighter Ideas Demonstration session, which is broadcast across all site functions. This offers the Spartronics Brooksville team members the opportunity to ask to pick their colleagues' brains, "cross-pollenate" ideas, and learn from each other. The session also sparks ideas in other team members and encourages teams to seek solutions for obstacles they may face. It also gives Idea Leads and their teams the recognition they deserve– from leaders they may not have regular interaction with.
"It is a great way for our Brooksville team members – from all areas – to get involved and positively impact the electronic contract manufacturing facility. This program has motivated team members to look beyond what's in front of them and think about how they can make a difference with their leadership skills. It's truly been wonderful to watch the program grow and to see how excited the team is about participating," says Macintosh.
Expanding Engagement Across Spartronics
Since relaunching the new Brighter Ideas program, 60% of the Spartronics Brooksville shop floor employees have participated in the program, and over 70% of ideas have been fully implemented or closed. These ideas range from something as simple as adding a scanner to save inspectors time daily, to cost savings for the facility and customer.
“The Brighter Ideas program fosters an environment in which employees have an authentic voice which can be heard throughout the organization. It allows employees to take a leadership role in resolving problems or improving processes - which gives them a sense of purpose and belonging. The Brighter Ideas program also provides recognition for their contributions and successes,” says Production Manager, Mark Butterfield.
While the former program only contributed about eight ideas per year, the new Brighter Ideas program was highly anticipated and has seen much higher engagement. In the program's first year, there were 85 idea submissions – over 10x more ideas than years prior! Moving from 2021 and into 2022, Spartronics Brooksville has had 137 ideas submitted to the Brighter Ideas program.
Whether big or small, the program has achieved its goal of getting employees to solve problems in their area, think strategically, and act as leaders. In addition, it has fostered positive change within the facility, saving employees, the facility, and customers time and money. The program has gained recognition throughout the Spartronics organization and will be implemented in other facilities. The Spartronics Brooksville Brighter Ideas program is undoubtedly the gold standard for upcoming programs in early 2023.
About Spartronics Brooksville
Spartronics Brooksville is a Center of Excellence in the electronic contract manufacturing (CM) of mission-critical applications for original equipment manufacturers (OEMs). Located in Brooksville, Florida, outside of Tampa, the facility performs all core functions from prototyping through production, featuring the most advanced processing technology coupled with extensive testing capabilities for manufacturing highly regulated complex products and systems. For more information, please visit Spartronics.com.